The Complete Guide to Diamond Cut Off Blade for Alumina
When it comes to cutting through extremely hard materials like alumina ceramic, ordinary cutting tools simply won’t make the grade. The exceptional hardness and brittleness of alumina demand specialized cutting solutions that can deliver precision, efficiency, and clean edges without damaging the material. This is where high-quality diamond cut off blades for alumina become indispensable tools for professionals across various industries.
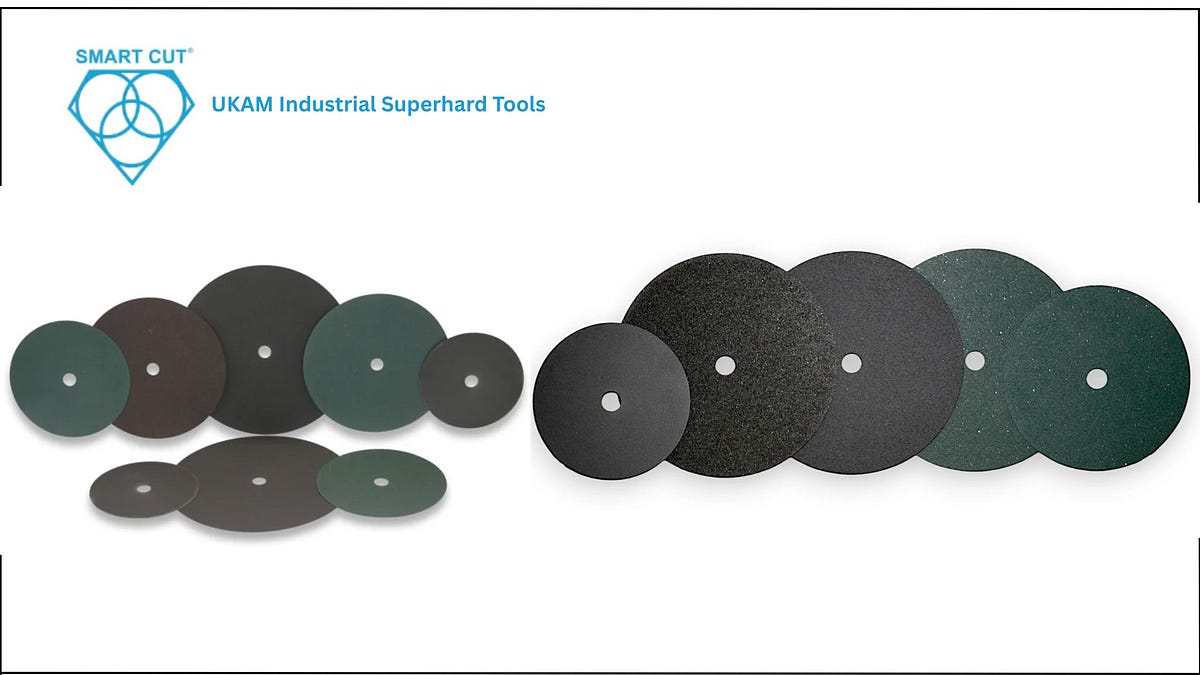
Understanding the Unique Properties of Alumina
Alumina (aluminum oxide) has earned its reputation as one of the most widely used technical ceramics thanks to its remarkable properties:
- Extreme hardness (9 on the Mohs scale)
- Excellent electrical insulation
- High thermal resistance (up to 1750°C)
- Superior wear resistance
- Chemical inertness
- Excellent compression strength
These properties make alumina ideal for countless applications — from electronic substrates to medical implants, and aerospace components to cutting tools. However, these same qualities create significant cutting challenges that only specialized diamond cutting tools can effectively overcome.
Why Diamond Blades Are Essential for Cutting Alumina
The exceptional hardness of diamond (10 on the Mohs scale) makes it the only practical material for effectively cutting alumina without excessive tool wear or material damage. High-precision diamond cut off blades for ceramic alumina offer several crucial advantages:
Superior Cutting Performance
Diamond particles embedded in the cutting edge easily slice through the hard alumina structure, maintaining sharpness far longer than conventional abrasive materials.
Minimized Material Damage
Quality diamond blades reduce the risk of chipping, cracking, or creating microfractures in the brittle alumina material — a critical factor for maintaining structural integrity in precision components.
Temperature Control
Advanced diamond blades dissipate heat effectively during the cutting process, preventing thermal shock that could compromise the alumina’s properties or dimensional stability.
Enhanced Productivity
The durability and consistent cutting performance of diamond blades translate directly to improved throughput, reduced downtime, and lower overall production costs.
For applications involving other superhard materials, specialized options like Diamond Cut Off Wheel Boron Nitride provide complementary cutting solutions that follow similar principles with adaptations for specific material properties.
Key Factors in Selecting the Right Diamond Blade for Alumina
Not all diamond blades are created equal, especially when it comes to cutting challenging materials like alumina. Several critical factors should guide your selection process:
Bond Matrix Composition
The material that holds the diamond particles in place significantly affects cutting performance:
- Resin Bonds: Offer excellent finish quality and cooler cutting, ideal for precision applications where surface finish is paramount.
- Metal Bonds: Provide superior durability and heat resistance, perfect for production environments requiring extended blade life.
- Hybrid Bonds: Combine advantages of both systems for balanced performance across multiple cutting parameters.
Diamond Concentration and Quality
Higher diamond concentration generally translates to more efficient cutting and longer blade life when working with extremely abrasive materials like alumina. However, quality matters just as much as quantity:
- Premium diamond particles maintain their cutting edges longer
- Consistent diamond size distribution ensures uniform cutting performance
- Optimal diamond exposure maintains cutting efficiency throughout the blade’s life
Blade Configuration
Different alumina applications may require specific blade configurations:
- Continuous Rim: Provides the smoothest possible edge finish for thin alumina substrates and precision applications
- Segmented: Offers enhanced cooling and swarf removal for thicker alumina pieces and higher-volume cutting
- Custom Configurations: Specialized designs for unique alumina applications with specific cutting requirements
Optimizing Cutting Parameters for Alumina
Even the highest quality diamond blade requires proper operating parameters to deliver optimal results on alumina:
Speed Considerations
Contrary to conventional wisdom, cutting alumina often benefits from moderate blade speeds rather than maximum RPM:
- Lower blade speeds typically generate less heat
- Reduced thermal stress minimizes the risk of microcracking
- More controlled material removal often yields cleaner edges
Feed Rate Management
The hardness and brittleness of alumina demand careful attention to feed rates:
- Consistent, moderate pressure yields the best results
- Excessive feed pressure increases the chipping risk
- Insufficient pressure can lead to the glazing of the diamond blade
Coolant Application
Proper cooling is non-negotiable when cutting alumina with diamond blades:
- Consistent coolant flow prevents localized thermal stress
- Water-based coolants are typically sufficient for most applications
- Specialized coolants may benefit particularly challenging cutting scenarios
Common Challenges and Solutions When Cutting Alumina
Challenge: Edge Chipping
Solution: Reduce feed rate, ensure proper blade selection (often finer grit), and verify optimal blade speed. Consider a continuous rim blade for the cleanest possible edge.
Challenge: Premature Blade Wear
Solution: Verify adequate cooling, check for appropriate diamond concentration for alumina’s hardness, and ensure the bond matrix is suitable for this abrasive material.
Challenge: Insufficient Cutting Speed
Solution: Assess diamond exposure (blade may need dressing), verify the blade specification is appropriate for alumina, and check for proper machine setup including rigidity and alignment.
Advanced Diamond Blade Technologies for Alumina
The cutting-edge of alumina processing continues to evolve with innovative diamond blade technologies:
Nano-Diamond Particles
Ultra-fine diamond particles offer exceptional cutting precision and surface finish quality for the most demanding alumina applications.
Smart Bond Systems
Advanced formulations automatically adjust exposure rates as the blade wears, maintaining optimal cutting performance throughout the blade’s service life.
Specialized Core Designs
Engineered cores reduce vibration, improve cooling, and enhance overall stability during the alumina cutting process.
Industry-Specific Applications for Diamond Cut Off Blades on Alumina
Electronics Industry
Precision cutting of alumina substrates for circuits, components, and semiconductors where dimensional accuracy and edge quality are critical.
Medical Technology
Manufacturing of alumina-based implants, dental components, and surgical instruments requires biocompatibility and perfect surface finishes.
Aerospace and Defense
Production of specialty sensors, insulation components, and high-performance parts where material integrity cannot be compromised.
Scientific Instruments
Fabrication of precision components for analytical equipment, optical systems, and measuring devices with exacting tolerances.
Maximizing ROI on Diamond Cutting Equipment for Alumina
While quality diamond blades represent a significant investment, they deliver exceptional return on investment through:
- Extended tool life when properly maintained
- Reduced material waste from precise, clean cuts
- Lower labor costs from increased productivity
- Fewer rejected parts due to improved cut quality
- Minimized need for secondary finishing operations
Best Practices for Diamond Blade Maintenance
To maximize the performance and lifespan of your diamond cut off blades for alumina:
- Clean blades thoroughly after each use to remove alumina particles
- Store in a dry, protected environment
- Regularly inspect diamond exposure and overall condition
- Follow manufacturer recommendations for dressing procedures
- Document performance to identify optimal replacement intervals
Conclusion: The Critical Importance of Quality
When processing valuable alumina components, the quality of your diamond cut off blade directly impacts your results and bottom line. Investing in premium cutting tools from trusted manufacturers like UKAM Industrial Superhard Tools ensures consistent precision, reliability, and efficiency.
By understanding the specific requirements of alumina cutting applications and selecting the appropriate diamond blade technology, manufacturers can transform this challenging material into precisely finished components that meet the most demanding specifications across industries.
Comments
Post a Comment